Next Generation Bipolar Plates for Automotive PEM Fuel Cells
Por um escritor misterioso
Last updated 30 maio 2024
The results of a successful U.S. Department of Energy (DoE) funded two-year $2.9 MM program lead by GrafTech International Inc. (GrafTech) are reported and summarized. The program goal was to develop the next generation of high temperature proton exchange membrane (PEM) fuel cell bipolar plates for use in transportation fuel cell applications operating at temperatures up to 120 °C. The bipolar plate composite developed during the program is based on GrafTech’s GRAFCELL resin impregnated flexible graphite technology and makes use of a high temperature Huntsman Advanced Materials resin system which extends the upper use temperature of the composite to the DoE target. High temperature performance of the new composite is achieved with the added benefit of improvements in strength, modulus, and dimensional stability over the incumbent resin systems. Other physical properties, including thermal and electrical conductivity of the new composite are identical to or not adversely affected by the new resin system. Using the new bipolar plate composite system, machined plates were fabricated and tested in high temperature single-cell fuel cells operating at 120 °C for over 1100 hours by Case Western Reserve University. Final verification of performance was done on embossed full-size plates which were fabricated and glued into bipolar plates by GrafTech. Stack testing was done on a 10-cell full-sized stack under a simulated drive cycle protocol by Ballard Power Systems. Freeze-thaw performance was conducted by Ballard on a separate 5-cell stack and shown to be within specification. A third stack was assembled and shipped to Argonne National Laboratory for independent performance verification. Manufacturing cost estimate for the production of the new bipolar plate composite at current and high volume production scenarios was performed by Directed Technologies Inc. (DTI). The production cost estimates were consistent with previous DoE cost estimates performed by DTI for the DoE on metal plates. The final result of DTI’s analysis for the high volume manufacturing scenario ($6.85 /kW) came in slightly above the DoE target of $3 to $5/kW. This estimate was derived using a “Best Case Scenario” for many of the production process steps and raw material costs with projections to high volumes. Some of the process improvements assumed in this “Best Case Scenario” including high speed high impact forming and solvent-less resins, have not yet been implemented, but have a high probability of potential success.

Electronic Transport and Corrosion Mechanisms of Graphite-Like

Bridging Models at Different Scales To Design New Generation Fuel
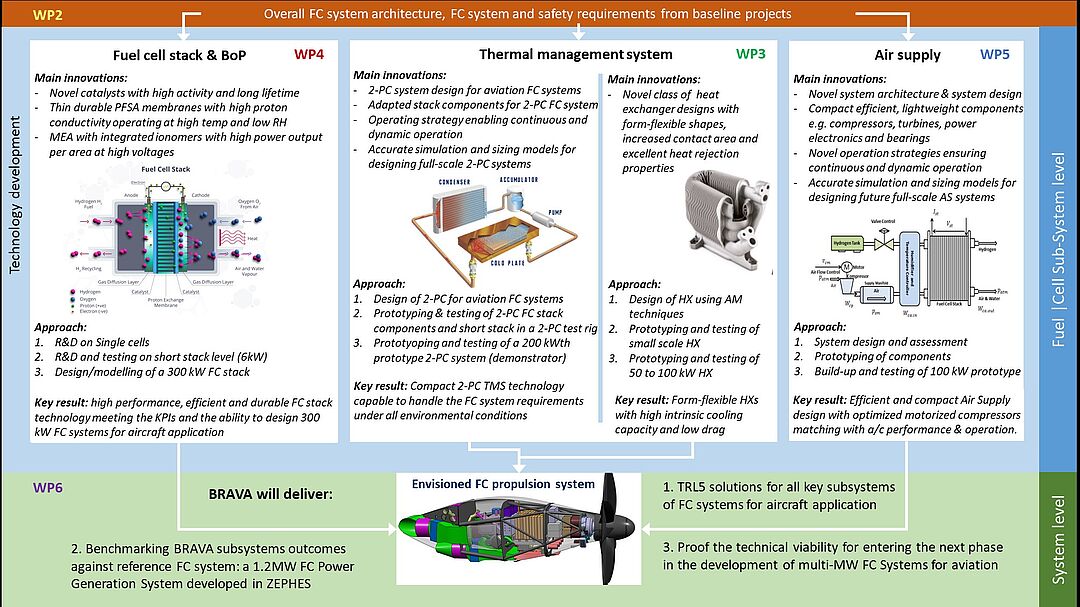
Research Projects
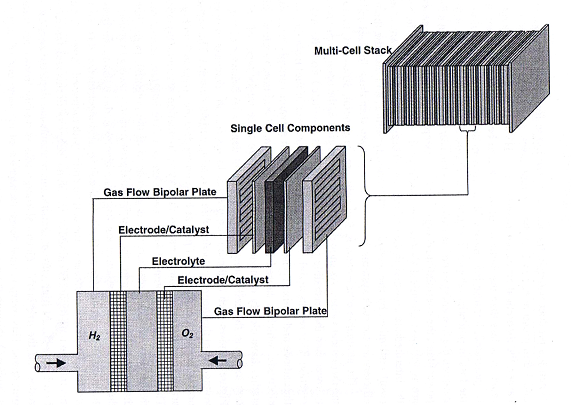
Electrochemistry Encyclopedia � PEM fuel cells
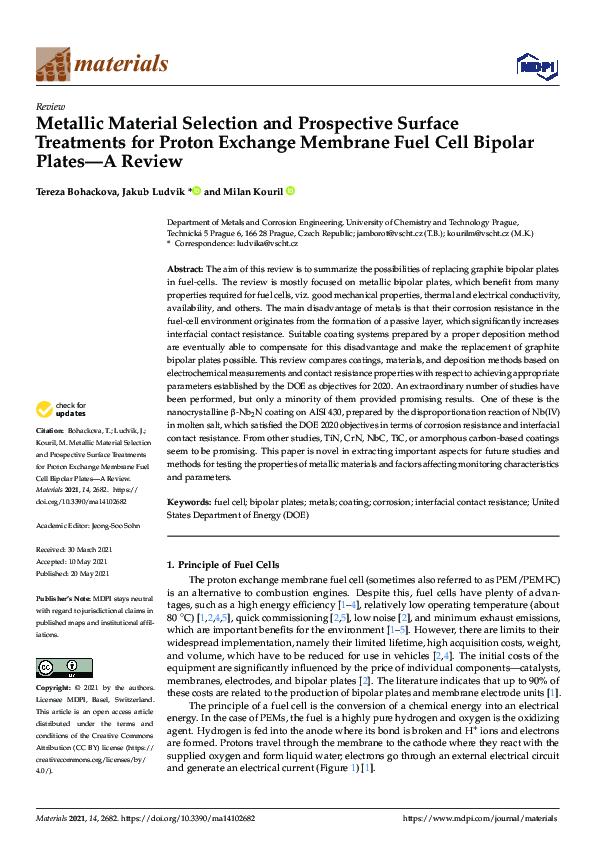
PDF) Metallic Material Selection and Prospective Surface

Fundamentals, materials, and machine learning of polymer

Low-Temperature Bipolar Plates
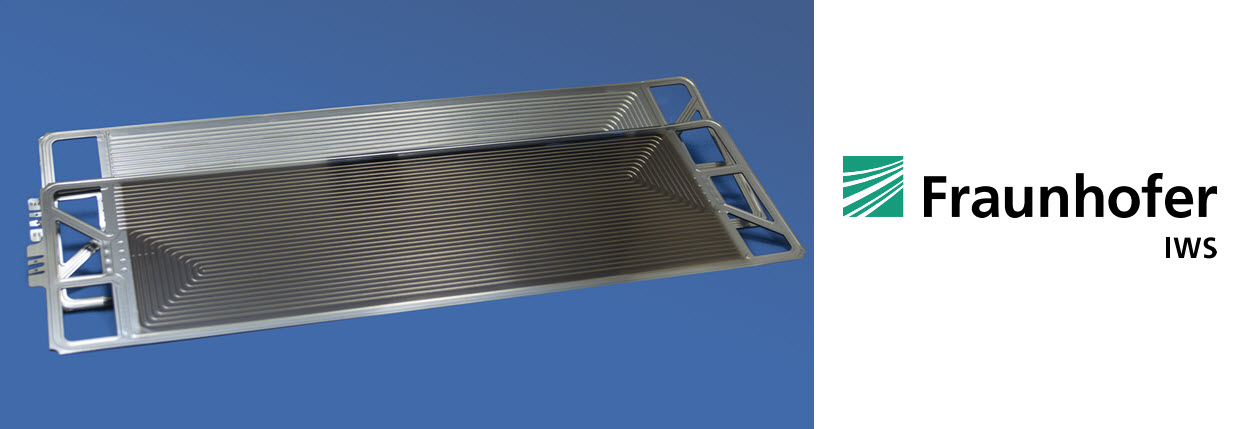
Graphite Instead Of Gold: Thin Layers For Better Hydrogen Cars
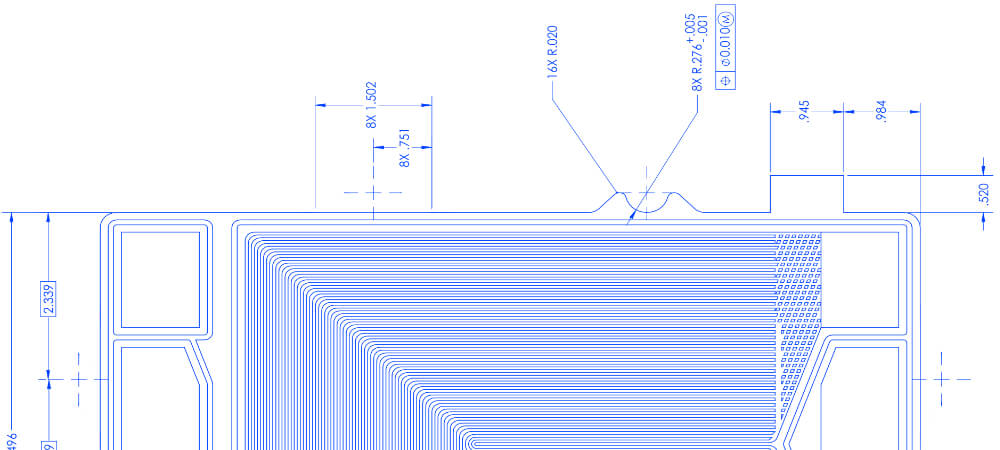
Bipolar Plates: Etching in Fuel Cell & Electrolyzer Technology
Recomendado para você
-
Project Proposal - prowe.30 maio 2024
-
Using the library The Warburg Institute30 maio 2024
-
Wiley Online Library Scientific research articles, journals30 maio 2024
-
Foreign Language Libraries30 maio 2024
-
SAS Libraries School of Advanced Study30 maio 2024
-
Utah's Online Library Tutorial - UEN30 maio 2024
-
WiFi Access Institute of Historical Research30 maio 2024
-
Miami gazette [1923-11-07 through 1924-03-05] - Magazines30 maio 2024
-
Research that matters: setting guidelines for the use and30 maio 2024
-
Erementar Gerade, Volume 11 by Mayumi Azuma · OverDrive: ebooks30 maio 2024
você pode gostar
-
21 Bares LGBT a não perder em Madrid30 maio 2024
-
SCP-173 Reading in the Shadows30 maio 2024
-
HOJE VAMOS JOGAR MUITOS JOGOS, PC EMPRESTADO RODANDO LISO . Contribua com meu tratamento. Qr code na tela. - alex_porto_ on Twitch30 maio 2024
-
Frases Aleatórias — via Oficina da Alma O mundo sempre gira, quero30 maio 2024
-
Siapa GMAN SKIBIDI TOILET 3.0 #skibiditoilet30 maio 2024
-
A Capivara Curitibana30 maio 2024
-
PROYAMA 58CC 2-Cycle Gas Powered Chainsaw, 16-Inch Top Handle Chain Saw, Gasoline Chainsaw 20-Inch for Tree Wood Cutting30 maio 2024
-
Jogo Titanfall (Legendado em Português) - Xbox 360 em Promoção na Americanas30 maio 2024
-
Caminhão arqueado wallpaper caminhão top Qualificado para Status30 maio 2024
-
Celebridades antes e depois da cirurgia plástica - MDig30 maio 2024